문 01. 용접기나 공작기계를 이용한 작업 시, 안전 주의사항에 대한 설명으로 옳은 것은?
① 선반 작업: 절삭 작업 중에 장갑을 착용해서는 안 된다.
② 연삭 작업: 회전하는 숫돌을 쇠망치로 강하게 타격하여 숫돌의 파손 여부를 확인한다.
③ 밀링 작업: 주축 회전수 변환은 주축의 이송 중에 수행한다.
④ 아크 용접 작업: 밀폐된 작업 공간에서는 KF94 마스크를 착용한다.
①
1번처럼 장갑끼고 하다가 회전하는거 터치하는 순간 그대로 말려들어가 끔찍한 일이 발생할 수 있다. 마찬가지로 머리카락도 조심해야 한다. 쏘우같은 일이 일어날지도 모른다.
<기계의 위험점>
1. 절단점
- 회전하는 운동부 자체, 운동하는 기계부분 자체의 위험점(날, 커터)
2. 물림점
- 회전하는 2개의 회전체에 물려 들어가는 위험점(롤러기기)
3. 협착점
- 왕복운동 부분과 고정 부분 사이에 형성되는 위험점(프레스, 창문)
4. 끼임점
- 고정부분과 회전하는 부분 사이에 형성되는 위험점(연삭기)
5. 접선물림점
- 회전하는 부분의 접선방향으로 물려 들어가는 위험점(밸트-풀리)
6. 회전말림점
- 회전하는 물체에 머리카락이나 작업봉 등이 말려 들어가는 위험점
문 02. 기하공차와 기호의 연결이 옳지 않은 것은?
④
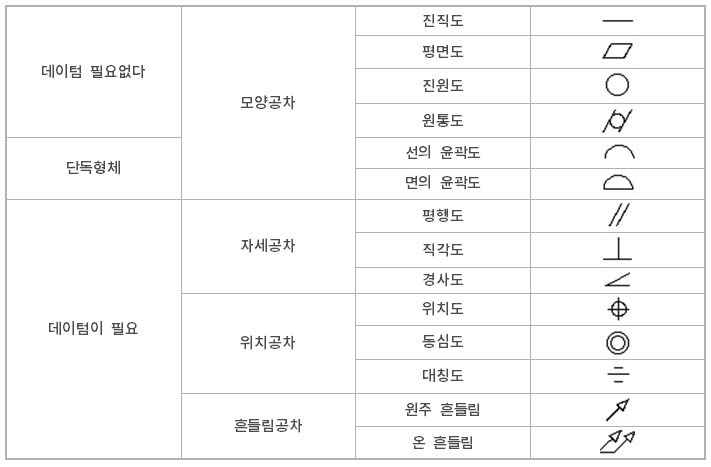
문 03. 산업용 로봇에서 링크, 기어, 조인트 등을 사용하여 인간의 팔과 손목 움직임을 구현하는 것은?
① 엔드 이펙터(end effector)
② 머니퓰레이터(manipulator)
③ 동력원(power source)
④ 제어시스템(control system)
②
<매니퓰레이터, manipulator>
인간의 팔이나 손의 기능과 유사한 역할을 수행하는 기구이다.
<엔드이펙터, end effector>
로봇의 손목 끝에 달려있는 작업공구를 의미하며 용접봉, 분무총(spray gun), 공구 또는 개폐식 여닫이를 가지는 집게(gripper 또는 finger) 등이 있다.
<겐트리, gantry>
로봇이 다리와 같은 프레임 위에 장착되었을 때 이것을 겐트리 로봇이라 일컬으며 다른 말로는 주행 형태(traverse type) 로봇이라고도 한다.
문 04. 일반적으로 압전 세라믹 소재가 적용된 부품이 아닌 것은?
① 광섬유
② 음향 마이크
③ 스트레인 게이지
④ 수중 음파 탐지기
①
<광섬유 재료>
일반적인 재료는 유리섬유이다. 이 유리섬유를 플라스틱으로 코팅한 막으로 구성하고 잘 구부러진다.
<광섬유 재료에 따른 분류>
1. 석영계 광섬유
- 코어부분은 실리카+GeO₂ 혹은 P₂O₅
- 클래드부분은 실리카+F 혹은 B₂O₃
2. 플라스틱계 광섬유
- 코어부분은 폴레메타이크릴산 메틸,
- 클래드에 불소함유 수지나 실리콘을 코팅 다성분계 광섬유
- 다라임 실리카, 보론 실리케이트
- 알루미나 실리케이트, 알칼리게르마노 실리케이트 결정 광섬유
- 사파이어, BaTiO₃, LiNbO₃
<세라믹, ceramics>
도기라는 뜻으로 점토를 소결한 것이며 알루미나 주성분에 Cu, Ni, Mn을 첨가한 것이다.
<세라믹의 특징>
- 세라믹은 1,200℃까지 경도의 변화가 없다.
→ 저온보다 고온에서 경도가 높아지는 것은 아니다.
- 고온경도가 우수하며 열전도율이 낮아 내열제로 사용된다.
- 냉각제를 사용하면 쉽게 파손되므로 냉각제는 사용하지 않는다.
- 세라믹은 이온결합과 공유결합 상태로 이루어져 있다.
- 세라믹은 금속과 친화력이 적어 구성인선이 발생하지 않는다.
- 충격에 약하고 금속산화물, 탄화물, 질화물 등 순수 화합물로 구성된다.
- 원료가 풍부하기 때문에 대량 생산이 가능하다.
- 불순물에 가장 크게 영향을 받는 기계적 성질은 횡파단강도이다.
문 05. 내열성이 좋으며 고온강도가 커서, 내연기관의 실린더나 피스톤 등에 많이 사용되는 것은?
① 인바
② Y 합금
③ 6 : 4 황동
④ 두랄루민
②
<인바, invar>
Fe-Ni 36%의 합금으로서 상온에 있어서 선팽창계수(길이방향)가 대단히 적고, 내식성이 매우 좋다. 주로, 줄자, 표준자, 시계의 추, 온도조절용 바이메탈 등의 재료로 쓰인다.
<6:4황동, muntz metal, 문쯔메탈>
- 6:4 황동은 600℃ 이하에서 가공 가능
- Zn 40%일 때 인장강도 최대
- 열전도 전기전도는 Zn 34%까지 낮아지다가 50%에서 최대
- 경년변화, 시간경과에 따라 경도 등 악화 됨
- α+조직, 탈아연 부식(Cl이 원인)
- 전연성이 낮고 인장강도는 크다.
- 내식성이 다소 낮지만 타 황동에 비해 값이 싸다.
<쾌삭황동, 납황동>
- 6:4황동 + Pb, 절삭성 우수, 나사, 볼트 재료
<네이벌 황동>
- 6:4황동(문쯔메탈) + Sn(1%), 용접용 파이프 재료
<델타 메탈, delta metal>
6:4황동에 Fe, Mn, Ni 등을 넣어서 여리지 않고 더욱 강력하며 또 내식성, 내해수성을 증가한 것을 고강도 황동 또는 망간청동이라고 한다. 6:4황동에 1% Fe을 함유한 것을 델타메탈(철황동)이라 하고 강도와 내식성이 좋다. 7:3황동에 2% Fe와 소량의 Sn, Al을 넣은 것을 듀라나 메탈(durana metal) 이라 하고 주조재, 가공재로 사용한다.
<망가닌>
- 6:4황동 + Mn(10%), 고유저항 저항온도계수, 전기저항 변화 극히 작음
<Al-Cu-Mg계 합금>
- 두랄루민(duralumin, 2017 합금)
- Al-Cu-Mg-Mn 합금(Cu 4%, Mg 0.5%, Mn 0.5%)
- 항공기 재료로 적합, 고온에서 물에 급랭하여 시효경화
- 인장강도 294~441 MPa
<Y합금, Y-alloy>
4% Cu, 2% Ni, 1.5% Mg의 Al 합금이다. 시효경화성이 있는 내열용 알루미늄 합금으로, 열간단조, 압출가공이 쉬우며 단조품, 피스톤 등에 이용된다. 고용체중에 3원 화합물인 Al₅Cu₂Mg₂가 경화 석출물로 되어 열처리에서 석출경화한다.
문 06. 스테인리스강에 대한 설명으로 옳지 않은 것은?
① 크롬계와 크롬-니켈계 등이 있다.
② 석출경화형계는 성형성이 향상되나 고온강도는 저하된다.
③ 크롬을 첨가하면 내부식성이 우수해진다.
④ 나이프, 숟가락 등의 일상용품과 화학공업용 기계설비 재료로 사용된다.
②
<석출경화형, PH형, 600계열>
크롬, 니켈, 철, 구리, 알루미늄, 티타늄, 몰리브덴으로 이루어져 있으며 내부식성, 고온강도, 연성이 좋다. 항공 우주구조용 부품에 사용된다.
문 07. 강의 공석변태와 조직에 대한 설명으로 옳지 않은 것은?
① 시멘타이트의 탄소 함유량은 6.67%이다.
② 페라이트와 시멘타이트의 혼합 조직은 마르텐사이트다.
③ 공석 반응점에서 오스테나이트가 페라이트와 시멘타이트로 변한다.
④ 0.77% 탄소강을 $A_{1} $변태온도 이하로 냉각하면 발생한다.
②
<공석강(eutectoid steel, 탄소량 = 0.76 ~ 0.86>
오스테나이트가 결정 경계부분부터 공석 반응을 일으켜 723℃에서 조직 전체가 공석 페라이트와 공석 시멘타이트로 변화된다. 이 두 조직은 층상으로 형성되는데 이렇게 형성된 조직을 펄라이트라고 한다.
<평형상태도에서 나타나는 반응>
공석: γ → α + Fe₃C, 0.77C , 723℃ , 펄라이트(오→페시=펄) A₁
공정: 액 → γ + Fe₃C, 4.3C , 1,130℃, 레데뷰라이트
포정: δ + 액 → γ , 0.17C , 1,495℃
자기변태점(큐리점, A₂): 768℃
왼 → 오(냉각)
공석 고 고고(냉각x)
공정 액 고고
포정 액고 고
편정 액 고액
문 08. 잔류응력(residual stress)에 대한 설명으로 옳지 않은 것은?
① 소재의 불균일 변형으로 발생한다.
② 추가적인 소성변형을 통하여 제거하거나 감소시킬 수 있다.
③ 외력이 제거된 상태에서 내력의 정적 평형조건이 만족하도록 분포된다.
④ 표면의 압축 잔류응력은 소재의 피로수명과 파괴강도를 저하시킨다.
④
숏피닝(shot peening)이나 표면압연(surface rolling)을 통해 재료의 표면에 압축잔류응력이 남게 되어 재료의 피로강도가 높아진다.
문 09. 용적식 펌프로 분류되지 않는 것은?
① 터빈 펌프
② 기어 펌프
③ 베인 펌프
④ 피스톤 펌프
①
<용적형 펌프>
- 왕복식(피스톤 펌프 = 플런저 펌프, 다이어프램 펌프, 버킷 펌프)
- 회전식(기어 펌프, 나사 펌프, 베인 펌프, 캠 펌프, 스크류 펌프)
<비용적형 펌프, 터보형 펌프>
- 원심식(벌류트 펌프, 터빈 펌프)
- 사류 펌프, 축류 펌프
- 축사벌터
<특수펌프>
- 재생펌프, 제트펌프, 기포펌프, 수격펌프
문 10. 적시 생산방식(just-in-time production)의 특징이 아닌 것은?
① 주문이 있을 때 부품과 제품을 생산하는 수요시스템(pull system)이다.
② 무재고 생산 또는 반복되는 대량생산 공정에 효과적이다.
③ 재고 운반 비용은 늘어나지만 부품검사와 재작업 필요성은 감소한다.
④ 생산을 허가하는 생산카드와 다른 작업장으로 운반을 허가하는 이송카드를 사용한다.
③
<적시생산방식, JIT: Just In Time>
- 재고를 쌓아 두지 않고서도 필요한 때 제품을 공급
- 다품종 소량 생산 체제의 구축 요구에 부응
- 적은 비용으로 품질을 유지
<JIT의 특징>
- 출고되는 제품의 양에 따라 필요한 모든 재료들이 결정
- 생산통제는 당기기 방식(Pull System)
- 생산이 소시장 수요를 따름
- 즉 계획을 일 단위로 세워 생산하는 것
- 생산공정이 신축성을 요구
- 신축성은 생산제품을 바꿀 때 필요한 설비
- 공구의 교체 등에 소요되는 시간을 짧게 하는 것을말함
- 큰 로드(lot) 규모가 필요 없으며 생산이 시장수요만을 따라감
→ 때문에 고속의 자동화는 필요하지 않음
- 작은 로트 규모를 생산하기 위하여 매일 소량씩 원료 혹은 부품이 필요
→ 공급자와의 밀접한 관계가 요구
<JIT의 기본요소>
소규모 생산과 제조준비시간 단축
- 문제점은 기계의 고장, 폐기물, 과다한 재공품, 검사의 지연
<생산의 평준화>
- 대생산일정계획(MRS)과 생산의 평준화가 이루어져야 함
- 생산계획 및 일정계획에 의하여 달성
- 제조공정 재설계로 로트 크기와 제조준비시간을 단축하여 달성
<작업자의 다기능화>
- 작업자들이 다수의 기능을 보유
- 즉 숙련자들이어야 함
<품질경영>
- JIT시스템의 능력은 기업의 높은 품질수준을 유지하는 것
- 품질면에서 설계품질, 규격과 설계의 적합성
- 신뢰성과 내구성, 기술적 탁월성을 제공
<간판시스템의 운용>
- 후속 제조공정이 선행 제조공정으로부터 부품 등 자재를 끌어가는 인출시스템
<JIT의 효과>
- 재고의 감소, 품질의 향상
- 문제의 원인을 조기에 발견하고 즉시 해결책을 강구할 수 있음
- 인원의 절감, 재작업의 감소, 자재낭비의 감소
- 생산성 향상, 자원의 낭비를 제거하므로 생산성의 향상을 가지고 옴
- 동기부여, 상호협조적인 분위기를 조성
문 11. 축의 치수가 $\oslash 100_{+0.1} ^{+0.15} $mm이고 구멍의 치수가 $\oslash 100_{0} ^{+0.07} $mm인, 축과 구멍의 끼워맞춤 종류는?
① 헐거운끼워맞춤
② 중간끼워맞춤
③ 억지끼워맞춤
④ IT끼워맞춤
③
구멍의 최대 크기보다 축의 최소 크기가 더 큼
문 12. 자동차 엔진에서 피스톤의 왕복 운동을 회전 운동으로 바꾸는 기계부품은?
① 차축
② 스핀들
③ 크랭크축
④ 플렉시블축
③
문 13. 선반 가공에서 발생하는 연속칩에 대한 설명으로 옳지 않은 것은?
① 취성이 높은 재료를 낮은 절삭속도로 가공할 때 발생한다.
② 연속칩이 생기는 경우 일반적으로 표면 거칠기 값이 작아진다.
③ 연속칩이 발생하면 칩이 공구에 감기는 문제가 발생할 수 있다.
④ 공구와 칩 사이의 마찰이 작으면 연속칩이 발생하기 쉽다.
①
<유동형 칩, 연속형 칩, continuous chip>
가장 이상적인 칩의 형태로서 일감이 깎여 나갈 때에 칩이 공구의 윗면을 원활하게 연속적으로 흘러나간다. 따라서 가공면이 깨끗하고 절삭력의 변동도 적으며 절삭작용이 원활하다. 발생조건은 아래와 같다.
- 연성재료를 고속절삭할 때
- 바이트의 윗면경사각이 클 때
- 절삭깊이가 작을 때
- 유동성 있는 절삭제를 사용할 때
<전단형 칩의 발생조건>
- 연성재료를 저속절삭 할 때
- 바이트의 윗면경사각이 작을 때
- 절삭깊이가 클 때
<열단형 칩>
칩이 공구의 날 끝에 붙어 원활하게 흘러가지 못하면 열단형 칩이 생성된다.
<균열형 칩, crack type>
불연속형 칩(discontinuous chip)이라고도 하며, 주철과 같은 취성이 큰 재료를 저속으로 절삭할 때 순간적으로 공구의 날끝 앞에서 일감에 균열이 일어나며 이때 발생하는 칩으로 진동때문에 날끝에 작은 파손이 생기고 깎여진 면도 매우 나쁘게 된다.
<균열형 칩의 발생>
- 주철과 같은 취성재료를 저속 절삭할 때
- 작은 경사각과 절삭깊이를 깊게 가공할 때
- 진동 때문에 날 끝에 작은 파손이 생겨 채터가 발생할 확률이 큼
문 14. 선삭용 단인 공구의 여유각에 대한 설명으로 옳은 것은?
① 칩 유동 방향과 공구 끝단의 강도를 조절한다.
② 양의 여유각은 절삭력과 절삭온도를 감소시킨다.
③ 공구강도와 절삭력에 영향을 미친다.
④ 공구와 공작물의 접촉 부위에서 간섭과 마찰에 영향을 준다.
④
경사각은 칩과의 마찰 및 흐름을 좌우하고 여유각은 공작물의 가공면과 공구와의 마찰을 감소하기 위한 각이다. 1, 2번은 경사각에 대한 설명이고, 3번은 전단각과 옆날각
<여유각, relief angle>
- 여유각이 없으면 날 자체가 물체에 손상을 입힐 수도 있다.
- 공구와 공작물 접촉 부위에서 간섭과 미끄럼 현상에 영향을 준다.
- 여유각은 바이트 날이 물체와 닿는 면적을 줄여준다.
→ 물체와의 마찰을 감소시키고 날 끝이 공작물에 파고들기 쉽게 한다.
- 깊게 절삭하고 싶을 때는 여유각을 좀 더 많이 주면 된다.
→ 여유각을 너무 많이 주게 되면 그 만큼 날 끝의 강도는 약해진다.
- 강도가 강한 재료일때는 여유각을 작게 해야 한다.
→ 여유각을 크게 하면 인선강도가 감소하여 공구 수명에 불리하다.
- 알루미늄, 연강 등 연성재료의 절삭가공 할 때는 크게 하는 것이 좋다.
- 전단각의 영향과 비슷하므로 같이 병행해서 보도록한다.
<여유각이 클 때의 영향>
- 가공시 에너지가 감소하고, 공구마멸이 감소한다.
- 인선강도가 감소하여 공구수명에 불리하다.
- 바이트의 앞면 및 측면과 공작물의 마찰이 최소화된다.
→ 플랭크 마멸이 약해진다.
- 절삭날 파손의 위험이 증가한다.
- 공구수명을 단축시키는 요인 중 하나인 치핑(chipping) 원인이 된다.
<여유각이 작을 때의 영향>
- 여유각이 작으면 떨림의 원인이 된다.
- 플랭크 마모가 증가한다.
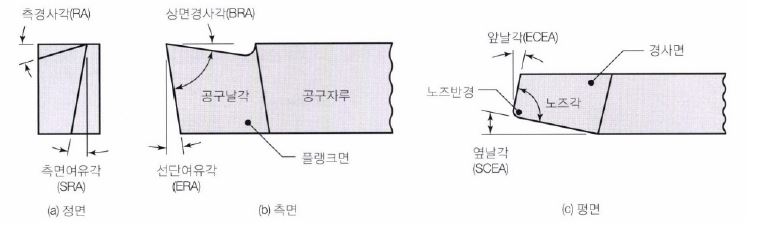
문 15. 형단조에서 예비성형을 하는 목적으로 옳지 않은 것은?
① 후속 단조공정에서 금형 마모를 줄이기 위해서
② 후속 단조공정에서 제품의 품질을 향상시키는 단류선을 얻기 위해서
③ 후속 단조공정에서 플래시로 빠져나가는 재료의 손실을 최소화하기 위해서
④ 후속 단조공정에서 변형률 속도(strain rate)를 높여 유동응력을 줄이기 위해서
④
<형단조에서 예비 성형을 하는 이유>
- 결함이 없는 재료 유동과 적절한 금형 충전을 유도
- 금형 마모의 감소 → 금형의 수명 증가
- 원하는 단류선을 얻어서 제품 품질 향상
- 플래시(flash)로 재료가 손실되는 것을 최소화
<에징, edging>
형단조(impression die forging)의 예비성형 공정에서 오목면을 가지는 금형을 이용하여 최종 제품의 부피가 큰 영역으로 재료를 모으는 단계
<형단조 예비 가공, preforming operations>
- 소재 블랭크(blank)의 준비
- 압출이나 인발된 소재에서 절단
- 예비 성형품(preform) 제작
- 분말야금, 주조, 예비 단조
<재료가 쉽게 다이의 공동부를 채울 수 있도록 미리 시행하는 작업들>
- 풀러링(fullering): 재료를 분산시키는 작업
- 에징(edging): 재료를 한 곳으로 모으는 작업
<단류선>
한방향으로 가공하면 섬유상조직이 나타나게 되어 강도가 증대한다. 이것은 결정립 변화로 인한 냉간가공의 특징이므로 알아두자. 예비 성형은 냉간가공 과정이기 때문에 변형률 속도(strain rate)를 높여도 유동응력의 변화가 거의 없다.
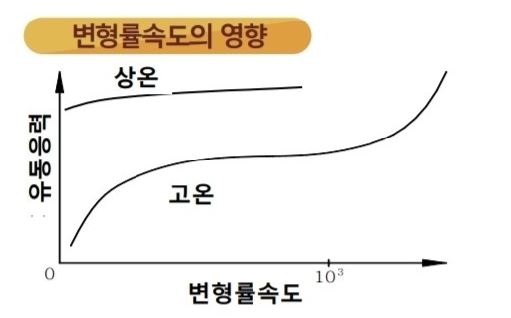
문 16. 결합용 기계요소인 핀(pin)에 대한 설명으로 옳지 않은 것은?
① 키 대신 사용되기도 하고, 코터가 빠져나오지 못하도록 고정하거나 부품의 위치를 결정하는 데 사용된다.
② 분할핀은 너트의 풀림 방지용으로 사용된다.
③ 주로 인장하중을 받아 파괴되며, 인장강도 설계가 중요하다.
④ 평행핀, 테이퍼핀, 분할핀 등이 있다.
③
핀은 전단강도가 중요
<나사의 풀림 방지법>
- 와셔에 의한 방법(스프링, 고무, 톱니붙이, 혀붙이 등)
- 플라스틱 플러그에 의한 방법
- 로크너트에 의한 방법(더블너트, 고정너트)
- 철사를 이용하는 방법
- 분할핀에 의한 방법
- 멈춤나사에 의한 방법
- 자동죔너트에 의한 방법(절입너트)
세로드립 와플로철분먹자
문 17. 수평으로 설치된 평벨트 전동장치에 대한 설명으로 옳지 않은 것은?
① 벨트와 작은 풀리의 접촉각이 증가하면 최대 전달동력이 증가한다.
② 바로걸기의 경우, 장력 차로 인한 접촉각 감소를 방지하기 위해 긴장측이 위쪽에 위치하도록 회전 방향을 결정한다.
③ 가죽 평벨트를 사용하는 경우, 속도비를 일정하게 유지하기 어렵다.
④ 축 중심 간 거리가 먼 경우, 고속으로 벨트전동을 하면 플래핑(flapping) 현상이 발생할 수 있다.
②
바로걸기에서 벨트를 수평으로 걸어서 전동하는 경우 긴장측을 아래쪽으로 하고 이완측을 위쪽으로 하면 접촉각이 크게 되어 미끄럼이 적게 된다. 그런데 두 개의 스프로켓이 수평으로 설치된 체인 전동장치는 긴장측이 위다.
<크리핑>
벨트가 풀리 림면을 기어가는 현상, 벨트에 작용하는 이완측 장력과 긴장측 장력의 차이로 인해, 긴장측 장력이 더 크기 때문에 이완측을 땡기므로 이완측이 슬슬 기어온다. 장력차에 의해 속도가 늦어지므로 벨트가 풀리의 림면을 기어간다.
<플래핑>
벨트가 파도치며 덜덜 거리는 현상, 축간거리가 길고 너무 고속으로 움직일 때 발생이 두 가지 원인으로 종동 풀리는 약 2~3%의 슬립이 발생한다. 풀리의 접촉각이 커지면 더 큰 동력전달이 가능함. 이런 이유로 엇걸기가 더 접촉각이 커서 더 큰 동력전달 가능. 하지만 벨트가 비틀리기 때문에 마멸하기가 쉽다. 또한, 벨트의 너비가 넓다면 더 많이 비틀리기 때문에 너비는 가능한 좁게 설계한다.
문 18. 사출성형에 대한 설명으로 옳지 않은 것은?
① 게이트는 용융 수지가 금형 공동으로 주입되는 입구이며, 하나의 금형 공동은 복수의 게이트를 둘 수 있다.
② 성형품의 수축결함을 방지하기 위해 사출 압력을 증가시키고, 성형 온도는 감소시킨다.
③ 열가소성 수지뿐 아니라 열경화성 수지를 이용한 제품 생산에도 사용될 수 있다.
④ 금형 내부에는 고온의 수지를 식히기 위한 냉각라인이 있다.
②
<사출에서의 수축량>
$ \delta = \frac{fW}{PTs} $
f=냉각시간, W=두께, 크기, P=사출압력, T=성형온도, s=가압시간(성형시간)
너무 급랭하면 열응력 발생시키므로 적당히 빠르게 냉각
<플라스틱의 가공공정: 열가소성 수지>
- 압출성형(열성형, 블로우성형 혹은 취입성형)
- 사출성형, 회전성형
<플라스틱의 가공공정: 열경화성 수지>
- 열경화성 수지는 압축전사
- 압축성형, 전이성형(전사성형), 사출성형
문 19. 미끄럼 베어링 재료의 요구사항으로 옳은 것은?
① 축과 베어링 사이로 흡입된 작은 외부 입자들은 베어링 표면에 흡착되거나 박힐 수 있어야 한다.
② 유막 형성을 억제하여 낮은 마찰력을 제공하여야 한다.
③ 열응력을 최소화하기 위해 낮은 열전도율을 가져야 한다.
④ 일반적으로 축 재료보다 높은 탄성계수를 가져야 한다.
①
<미끄럼 베어링 재료의 요구사항>
- 내식성이 크고, 열전도율이 높아야 한다.
- 마모가 적고 피로강도가 높아야 한다.
- 마멸성이 적고, 마찰계수가 작아야 한다.
- 축 재료보다 낮은 탄성계수를 가져야 한다.
→ 축 재료보다 연질이어야 한다.
- 유막 형성이 쉽고, 오일 흡착력이 용이해야 한다.
- 하중에 견딜 수 있도록 충분한 압축(면압) 강도를 가져야 한다.
- 열붙음(녹아붙음)이 일어나기 어려워야 한다.
<베어링 재료로 사용하는 비금속 재료>
흑연, 플라스틱, 고무 등이 있다. 흑연은 고체 윤활제의 역할을 함으로써 별도의 윤활제가 필요하지 않다. 플라스틱은 윤활유가 없는 상태에서도 비교적 마찰 계수가 작고 내마멸성도 좋으며, 경계 윤활성이 좋아 베어링 재료로서 적합하다. 고무는 물과 같이 저점도 윤활제의 역할을 하며, 마찰 계수가 작고 진동, 충격의 흡수성이 우수하여 백 메탈(back metal)에 부착하여 사용한다.
문 20. 표면 공정 작업에 대한 설명으로 옳지 않은 것은?
① 무전해도금법(electroless plating)은 외부 전류 없이 화학적 반응만으로 도금하는 것으로, 복잡한 형상의 부품에서도 균일한 도금 두께를 얻을 수 있다.
② 아노다이징(anodizing)은 전해공정을 통해 산화피막을 가공물에 형성하는 것으로, 알루미늄 표면의 내식성이 향상된다.
③ 스퍼터링(sputtering)은 원하는 증착재료를 고온 가열하여 기화시켜 가공물의 표면에 증착하는 방법이다.
④ 유기코팅의 방법 중 딥코팅(dip coating)은 부품을 액상 코팅 물질이 담긴 탱크에 담그고 꺼내는 공정으로 수행된다.
③
<양극산화법, anodizing>
알루미늄에 많이 적용되며 다양한 색상의 유기 염료를 사용하여 소재 표면에 안정되고 오래가는 착색피막을 형성하는 표면처리 방법
<양극산화법, 아노다이징의 주된 목적>
산화알루미늄 Al₂O₃ 피막형성, 내식성 향상, 표면착색
<물리기상증착법, Physical Vapor Deposition, PVD>
PVD는 진공 중에서 전기에너지를 이용한 물리적 반응으로 증착을 형성시켜 박막을 기판 위에 증착시키는 기술이다.
<열증착법, thermal evaporation>
증착물질을 보트에 올려놓고 보트를 가열하여 증착물질을 증발시켜 기판에 증착시키는 방식이다. 단원소 물질의 증착에 주로 사용한다.
<전자빔증착법, e-beam evaporation>
열증발법과 유사하나 보트가열에 의한 열전달이 아니라 전자빔을 이용하여 증착물질을 가열 및 증발시키는 방식이다.
<스퍼터링, sputtering>
고에너지의 입자를 증착물질(타깃)에 조사하여 타깃의 구성원자가 타깃표면으로부터 방출되는 현상을 이용하여 타깃물질을 증착시키는 방식이다. 플라스마에 의해 타깃에 입사되는 알곤 이온이 발생되며 알곤 이온이 타깃과 충돌하여 타깃 내부 원자와 충돌하여 타깃으로부터 외부로 타깃 원자가 방출되어 기판을 전달되어 박막이 증착된다.
<딥 코팅, dip coating>
유기코팅의 방법 중 딥코팅은 부품을 액상 코팅 물질이 담긴 탱크에 담그고 꺼내는 공정으로 수행된다. 피도장물을 도료안에 담갔다가 빼서 건조시키는 도장법이며, 모양이 복잡하고 칠하기에 적당하지 않은 것이거나, 앞뒤가 같은 색인 것에 응용된다. 작업은 간단하지만, 탱크에 다량의 도료를 준비해 놓지 않으면 안 되며, 점성도를 항상 일정하게 해야만하는 등의 주의가 필요하다.
'기계일반 > 국가직 9급' 카테고리의 다른 글
2023년 국가직 9급 기계일반 문제 및 해설 (0) | 2023.04.08 |
---|---|
2022년 국가직 9급 기계일반 문제 및 해설 (0) | 2023.04.08 |
2020년 국가직 9급 기계일반 문제 및 해설 (0) | 2023.04.08 |
2019년 국가직 9급 기계일반 문제 및 해설 (0) | 2023.04.08 |
2018년 국가직 9급 기계일반 문제 및 해설 (0) | 2023.04.08 |
댓글