문 01. 〈보기〉와 같이 스프링을 이용하여 500kg의 물체를 매달았다. 이때 물체의 처짐량[mm]은? (단, 탄성계수 $k_1=100N/mm$, $k_2=150N/mm$, $k_3=300N/mm$이고, 중력 가속도는 10$m/s^2$이며, 스프링 질량은 무시한다.)
① 20
② 25
③ 30
④ 35
②
<스프링에 걸리는 하중>
$P=k \delta $
<계산과정>
1) 등가 스프링 상수 구하기
$k_{2} $와 $k_{3} $는 직렬로 연결되어 있다. 두 상수의 역수를 더한 후 다시 역수를 취해준 값은 $k_{e} =100N/mm$ 이다.
2) 최종 스프링 상수 구하기
$k_{1}$와 $k_{e}$는 병렬로 연결되어 있으므로 두 상수를 그냥 더하면 된다. 최종 상수값 $k =200N/mm$ 이다.
3) 처짐량 구하기
$P = 500 kg \times 10 m/s² = 5,000N = 200 N/mm \times δ mm$
$δ =25mm$
문 02. 금속을 소성영역까지 인장시켰다가 하중을 제거한 후 압축했을 때 압축 항복강도가 인장 시보다 작아지는 현상으로 가장 옳은 것은?
① 가공경화
② 시효 경화
③ 탄성 여효
④ 바우싱거 효과
④
<가공경화, work hardening, 변형경화, strain hardening>
슬립을 일으키는 데 필요한 전단응력의 크기는 전위로 인해 이론값보다 작지만, 전위가 많아지면 전위끼리 서로 간섭하여 얽히고, 결정립계, 불순물, 개재물에 의해 움직임이 방해된다. 즉, 전위의 움직임이 더 힘들어진다. 이 방법으로 전단응력을 증가시키는 것, 즉 금속의 강도가 높아지는 것을 가공경화(work hardening) 또는 변형경화(strain hardening)라고 한다. 변형이 심할수록 전위들의 얽힘도 증가하고, 금속의 강도도 증가한다. 가공경화는 상온에서의 금속 가공공정에서 금속의 강도를 높이는 데 잘 활용된다. 전형적인 예로, 인발에 의해 단면적을 감소시켜 선재의 강도를 높이거나, 단조로 볼트머리를 만드는 공정, 자동차차체용 박판 및 항공기 동체소재의 압연 등을 들 수 있다. 변형경화의 정도는 변형경화지수 n으로 나타낸다. 세가지 결정구조 중에서, HCP 구조의 n 값이 가장 낮고, BCC, FCC 구조의 순서로 높아진다.
<시효경화, age hardening>
어느 종류의 금속이나 합금은 가공경화한 직후부터 시간의 경과와 함께 기계적 성질이 변화하나 나중에는 일정한 값을 나타내는 현상을 시효경화라 한다. 황동, 강철, 두랄루민 등이 시효경화를 일으키기 가장 쉬운 재료이다.
<탄성여효, elastic after-effect>
외부에 장시간 방치하면 자연스레 시간에 따라 잔류응력이 감소하는 현상이다. 외력을 제거해도 순간적으로는 없어지지 않으므로 소멸하기까지 어느정도 시간을 필요로 한다. 탄성여효는 고체의 종류와 온도, 압력 등에 따라 다르게 나타날 수 있다.
<바우싱거 효과, bauschinger effect>
재료에 탄성 한계 이상의 하중을 한쪽에 가한 다음에 반대 방향에 하중을 가할 때는 처음부터 그 방향으로 하중을 가했을 때보다도 비례 한계 또는 항복점이 현저하게 저하하는 현상이다. 이것은 다결정 금속뿐만 아니라 단결정에도 존재한다.
문 03. 크리프 현상에 대한 설명으로 가장 옳지 않은 것은?
① 크리프는 재료에 높은 온도로 큰 하중이 일정하게 작용될 때 재료 내의 응력과 변형률이 증가되는 현상이다.
② 고온의 경우 시간의 경과에 따라 재료의 항복응력보다 훨씬 낮은 응력에서도 파단이 일어날 수 있다.
③ 크리프 한도 응력은 특정 온도에서 응력이 작용하여 일정시간 경과 후에 크리프 속도가 0이 되는 한계응력을 의미한다.
④ 일정한 온도에서 하중의 크기가 클수록 크리프 속도가 증가하여 파단에 이르는 시간이 짧아진다.
①
<크리프 현상>
크리프는 재료에 높은 온도로 큰 하중이 일정하게 작용될 때 재료 내의 변형률이 증가되는 현상이다. 고온의 경우 시간의 경과에 따라 재료의 항복응력보다 훨씬 낮은 응력에서도 파단이 일어날 수 있다. 크리프 한도 응력은 특정 온도에서 응력이 작용하여 일정시간 경과 후에 크리프 속도가 0이 되는 한계응력을 의미한다. 일정한 온도에서 하중의 크기가 클수록 크리프 속도가 증가하여 파단에 이르는 시간이 짧아진다.
<1차 크리프, 천이 크리프>
특정 온도가 되면 순간적으로 약한 부분에서 전위가 증식하여 변형이 시작된다. 시간에 따라 변형이 진행되고 변형률이 감소, 가공경화로 묶였던 전위가 고온에서 응력하에서 이동하여 변형이 진행되고 전위가 많아져 서로 엉키고 크리프 속도가 감소된다.
<2차 크리프, 정상 크리프>
일정한 변형률로 변형 진행, 가공경화와 회복(고온)에 의한 연화가 평형을 이루면서 크리프 속도가 일정하게 된다.
<3차 크리프, 가속 크리프>
시간에 따라 변형률이 증가하다 시료 파단, 원자공공 농도가 증가되어 원자확산이 빨라지고 전위이동 쉬워져 크리프 속도가 증가된다. 그리고 원자공공이 결정립계에 모여 공동이 결합되고 미세균열이 형성되어 파단된다. 주로 슬립에 의해서 파괴되고 중심부는 입계파괴가 일어날 수 있다.
<크리프 현상에 영향 미치는 조건>
온도가 높을수록, 응력이 증가할수록, 결정이 미세할수록 크리프 현상이 두드러짐, 즉 변형속도가 커진다.
<재료에 따른 크리프 곡선 특성>
순금속에서는 정상단계가 짧고 취성재료에서는 가속단계 없이 갑자기 파단된다.
<크리프 특성 표기법>
온도, 응력조건 표기
<크리프 강도>
일정온도, 일정한 하중에서, 크리프에 의해 기울기가 규정한 값에 이르는 응력
<파단강도>
어떤 규정된 시간에 크리프 파단을 나타내는 응력

문 04. 원동차 모듈 2, 원동차 잇수 48, 종동차 모듈 2, 종동차 잇수 16인 스퍼기어 한 쌍에서 원동차가 1분에 600번 회전할 때 종동차 회전수의 값[rpm]은?
① 600
② 900
③ 1,200
④ 1,800
④
<기어열에서의 개념원리>
공식도 좋지만, ZN = ZN 이용하기
<계산과정>
48 x 600 = 16 x N
문 05. 외접하는 원추마찰차에서 원동차의 원추각이 30°, 종동차의 원추각이 60°일 때 원동축의 각속도 $\omega _1$ rad/s에 대한 종동축의 각속도 $\omega _2$ rad/s의 회전속도비($ \frac{\omega _2}{\omega _1} $) 값은?
① $\frac{1}{2} $
② $\frac{1}{ \sqrt{3} } $
③ $\frac{ \sqrt{3} }{2} $
④ $ \sqrt{3} $
②
<외접 원추 마찰차>
$ \alpha $ = 원동차의 원추각, $\beta $ = 종동차의 원추각, $\alpha +\beta $ = 축각
$N_1$ = 원동차의 회전속도, $N_2$ = 종동차의 회전속도
$\frac{N_2}{N_1} = \frac{D_1}{D_2} = \frac{sin \alpha }{sin \beta } $
문 06. 총형가공법에 의한 기어절삭에 사용되는 절삭공구로 가장 옳은 것은?
① 피니언 커터
② 호브
③ 래크 커터
④ 브로치
④
<기어절삭법>
- 총형공구에 의한 절삭법(브로치)
- 형판에 의한 방법(모방절삭법)
- 창성법
- 전조에 의한 방법
<창성법, generation method>
- 래크 커터를 사용한 마그식 기어 셰이퍼
- 피니언 커터를 사용한 펠로즈식 기어 셰이퍼
- 호브(hob)를 사용한 호빙머신
→ 스퍼기어 헬리컬 기어 등을 깎을 수 있다.
문 07. 지름 10mm의 트위스트 드릴을 사용하여, 마그네슘 블록에 구멍을 뚫는 작업을 한다. 이송량이 0.1mm/rev, 스핀들의 회전수는 1,200rpm일 때 재료제거율의 값[$mm^3/s$]은? (단, $\pi $는 3이다.)
① 150
② 600
③ 3,000
④ 9,000
①
사실 이 문제는 암기가 필요없는게, 이해해보면, 재료제거율은 공작물이 얼마나 빠르게 들어가는지 계산하면 된다. 공구는 회전하고, 그 상태로 직선으로 투영면적에 들어가므로, 드릴이 직선으로 이동하는 속도를 곱해야 한다. 따라서 드릴의 회전속도를 구하지 않도록 주의하고, 투영면적의 넓이를 공구 이송속도 곱하면 답
<계산과정>
$v=0.1mm/rev \times 1,200rev/min=120mm/min=2mm/s$
$A= \frac{ \pi }{4} d^2= \frac{3}{4} \times 10^2=75mm^2$
문 08. 주조 공정 중 소모성 주형 주조 공정에 해당하지 않는 것은?
① 풀몰드법(full molding)
② 셸주조법(shell molding)
③ 원심주조법(centrifugal casting)
④ 인베스트먼트 주조법(investment casting)
③
<영구 주형 주조법 종류>
다이캐스팅, 가압주조법, 슬러시주조법
원심주조법, 스퀴즈주조법, 반용융성형법, 진공주조
- 다가슬 원스반진
<풀 몰드 주조 공정, full-mold casting process>
폴리스티렌(polystyrene)을 팽창시켜 만든 모형(pattern)이 있는 주형에 용융금속(molten metal)을 주입하여 폴리스티렌을 녹이고 그 자리를 용융금속이 채우면서 냉각되어 제품이 만들어지는 가공법
<셸 몰드법, shell molding>
금속으로 만든 모형을 가열하고 그 모형 위에 규사와 페놀계 수지를 배합한 가루를 뿌려 경화시켜 주형을 만드는 방법이며 주형은 상하 두 개의 얇은 조개 껍데기 모양의 셸로 만들어지므로 셸몰드 주조법이라 부른다. 사형주조법에 비하여 치수정밀도가 좋으며, 표면이 아름답다. 주로 소형 주조에 유리하고 대형 주조에는 적합하지 않으며 자동화가 가능하여 대량생산이 가능하다.
<원심 주조법, centrifugal casting>
속이 빈 주형을 수평 또는 수직상태로 놓고, 중심선을 축으로 회전시키면서 용탕을 주입하여 그때에 작용하는 원심력으로 치밀하고 결함이 없는 주물을 대량생산하는 방법이다. 이 공정에는 진원심주조, 반원심주조, 센트리퓨징의 세 가지 종류가 있다.
<원심 주조법의 특징>
- 용융금속에 높은 압력이 걸리게 되므로 주물의 조직이 치밀하게 된다.
- 수축공이나 기공이 없다.
- 비중차이에 의한 개재물의 분리제거가 가능하다.
- 주물 모양에 따라 다르지만, 탕구나 압탕이 필요하지 않다.
→ 재료의 회수율이 높다.
- 관이나 원통형의 주물을 만들 때에도 코어가 필요없다.
- 모형(패턴)이 필요없다.
- 작업시간이 짧고, 대량생산이 가능하다.
- 응고가 빠르거나 유동성이 작은 금속일수록 주형의 회전속도를 크게한다.
- 제품이 회전대칭일 필요는 없다.
<인베스트먼트법, investment process>
정밀주조법의 한 종류이며 납 등의 융점이 낮은 것으로 원형을 만들고 이 주위를 내화성이 있는 주형재인 인베스트먼트로 피복한 후 원형을 융해 및 유출시킨 주형을 사용한 주조법이다. 복잡한 형상의 주물, 기계 가공이 곤란한 합금 등의 주조에 적합하며 이 공법에서 만들어진 주물은 치수 정도가 높고, 주물 표면이 좋다.
문 09. 피복금속아크용접(Shielded Metal Arc Welding:SMAW) 에서 아크 용접봉 피복제의 역할로 가장 옳지 않은 것은?
① 슬래그를 발생시키고 용융금속의 유동성을 좋게 한다.
② 전류를 잘 통하게 하여 아크의 안정성을 좋게 한다.
③ 스패터링을 적게 한다.
④ 용접 중 산화 및 질화를 방지한다.
②
<피복제, flux>
용접용은 심선과 피복제(flux)로 구성되어 있다. 그리고 피복제의 종류는 가스 발생식, 반가스 발생식, 슬래그 생성식이 있다. 우선, 용접입열이 가해지면 피복제가 녹으면서 가스 연기가 발생하게 된다. 그리고 그 연기가 용접하고 있는 부분을 덮어 대기중으로부터의 산소와 질소로부터 차단해주는 역할을 한다. 따라서 산화물 또는 질화물이 발생하는 것을 방지해 준다. 또한, 대기 중으로부터 차단하여 용접 부분을 보호하고, 연기가 용접입열이 빠져나가는 것을 막아주어 용착금속의 냉각속도를 지연시켜 급랭을 방지해준다. 그리고 피복제가 녹아서 생긴 액체 상태의 물질을 용제라고 한다. 이 용제도 용접부를 덮어 대기중으로부터 보호하기 때문에 불순물이 용접부에 함유되는 것을 막아 용접 결함이 발생하는 것을 막아주게 된다. 불활성 가스 아크 용접은 아르곤과 헬륨을 용접하는 부분 주위에 공급하여 대기로부터 보호한다. 즉, 아르곤과 헬륨이 피복제의 역할을 하기 때문에 용제가 필요 없는 것이다.
용가제 = 용접봉과 같은 의미로 보면 된다.
<용접 피복제의 역할>
- 용융금속 중 산화물을 탈산하고 불순물을 제거하는 작용을 한다.
- 스패터를 적게 발생시키고, 아크의 발생과 유지를 안정되게 한다.
- 슬래그가 되어 용착금속의 급랭을 방지하여 조직을 좋게 한다.
- 용착금속의 흐름을 원활하게 하고, 용착금속을 보호한다.
- 용융금속의 용적을 미세화하여 용착효율을 높인다.
- 필요원소를 용착금속에 첨가시킨다.
- 수직이나 위보기 등의 어려운 자세를 쉽게 한다.
- 전기 절연 작용을 하고 용융금속의 유동성을 좋게 한다.
- 슬래그 박리성을 좋게 하고 파형이 고운 비드를 만든다.
- 용융금속의 응고와 냉각속도를 느리게 한다.
- 산화 및 질화를 방지하고 전기통전작용을 방지(억제)한다.
문 10. <보기>와 같이 집중하중 P가 작용하는 보에서의 BMD(Bending Moment Diagram, 굽힘 모멘트 선도)로 가장 옳은 것은?
③
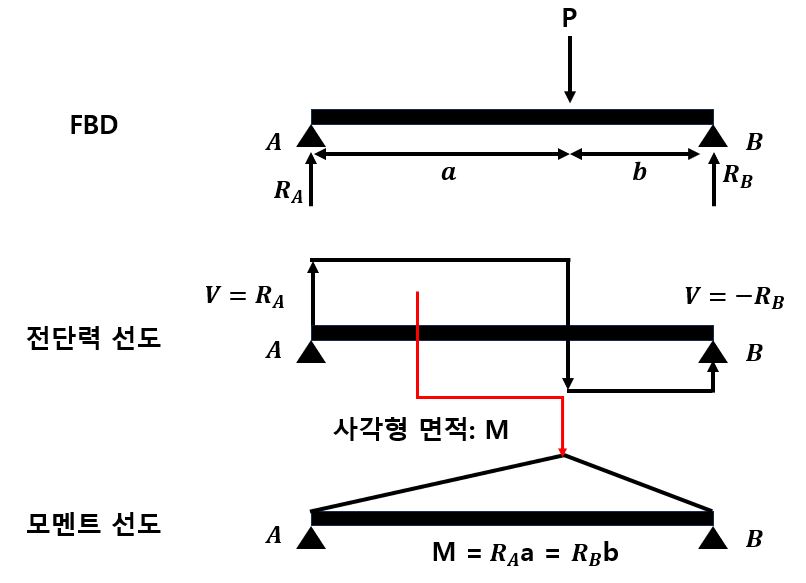
문 11. 절삭가공에서 다수의 절삭날을 가진 커터가 다양한 방향의 회전축을 중심으로 회전운동하며 공작물을 절삭하고, 평면 및 곡면을 가공하는 방법으로 가장 옳은 것은?
① 밀링(milling)
② 드릴링(drilling)
③ 태핑(tapping)
④ 리밍(reaming)
①
<밀링, milling>
절삭가공에서 다수의 절삭날을 가진 커터가 다양한 방향의 회전축을 중심으로 회전운동하며 공작물을 절삭하고, 평면 및 곡면을 가공하는 방법이다.
<드릴링, drilling>
구멍을 뚫는 작업. 구멍의 치수정확도와 표면정도를 향상시키려면 보링작업이나 태핑작업을 추가함
<태핑, tapping>
탭(tap)을 사용하여 암나사를 가공하는 자유단조 작업이다. (1번탭 55%, 2번탭 25%, 3번탭 20%)
<리밍, reaming>
드릴로 뚫어진 구멍이나 선삭가공품의 구멍의 형상과 치수를 리머를 사용하여 정밀하게 다듬질 하는 작업이다. 리밍을 하려면 드릴로 소요지름보다 작은구멍을 뚫은 후에 리머를 사용한다.
문 12. 용융된 금속이 모재와 잘 융합되지 않고 표면에 덮여 있는 상태로서 용접 속도가 느릴 때 발생하는 현상으로 가장 옳은 것은?
① 스패터
② 용입불량
③ 오버랩
④ 언더컷
③
<스패터, spatter>
용융상태의 슬래그와 금속내의 가스팽창폭발로 용융금속이 비산하여 용접부분 주변에 작은 방울형태로 접착되는 현상
<스패터의 원인>
- 아크과대
- 전류과다
- 용접봉 결함
<용입 부족, incomplete penetration>
완전히 용입되어야 하는 루트면이 용융되지 않고 남은 상태, 홈각도가 지나치게 작은 경우나 백가우징이 불충분한 경우에 루트면이 미용융 상태로 남아 발생한다. 루트 간격이 작은 경우에는 균열상이 되어 응집력이 커진다.
<용입부족의 원인>
- 홈 각도의 과소, 용접전류 과소
- 용접속도 빠를 때, 저항열이 클 때
- 부적합한 용접봉
- 모재에 다량의 황이 포함되어 있을 때
<오버랩, over lap>
용접봉의 용융점이 모재의 용융점보다 낮거나, 비드의 용융지가 작고 용입이 얕아서 비드가 정상적으로 형성되지 못하고 위로 겹쳐지는 현상
<오버랩의 원인, 전부 작을 때>
- 용접전류가 부족할 때
- 아크의 길이가 짧을 때
- 용접속도가 너무 느릴 때
- 부적당한 용접봉을 사용할 때
<언더컷, under cut>
모재의 일부가 과다한 전류 등에 의해 녹아서, 상부에 홈이 형성되는 것
<언더컷의 발생 원인, 전부 클 때>
- 용접 전류가 너무 높을 때
- 용접 속도가 너무 빠를 때
- 아크 길이가 너무 길 때
- 용접봉 선택이 부적당할 때
- 용접봉의 각도 및 운봉이 부적절할 때
문 13. <보기>와 같이 스프링 상수(k)는 900N/m이고, 질량(M)은 100kg인 1자유도 시스템이 있다. 초기 변위는 0이고 스프링 변형량도 없는 상태에서 방향으로 3m/s의 속도로 움직이기 시작한다고 가정할 때 이 시스템의 고유진동수 값[Hz]은? (단, $\pi $는 3으로 하고, 마찰력과 스프링 질량은 무시한다.)
① 0.25
② 0.5
③ 0.75
④ 1.0
②
<고유진동수> <변위>
$2 \pi f= \omega = \sqrt{ \frac{k}{m} } $ $x=x_0sin \omega t$
f = 헤르츠(Hz), 주기 T는 헤르츠의 역수
<계산과정>
$2 \pi f= \sqrt{ \frac{k}{m} } = \sqrt{ \frac{900N/m}{100kg} } =3rad/s$
$f(Hz)= \frac{3rad/s}{2 \pi }=0.5$
문 14. 두 축이 서로 교차하지도 않고 평행하지도 않을 때 동력을 전달하는 기어로 옳은 것은?
① 하이포이드 기어
② 스파이럴 베벨기어
③ 마이터 기어
④ 헬리컬 기어
①
<두 축이 평행한 기어>
- 스퍼 기어, 인터널 기어, 랙, 헬리컬 기어, 이중 헬리컬 기어, 내접 기어, 헤링본 기어
<두 축이 교차하는 기어>
- 직선 베벨 기어, 스파이럴 베벨 기어, 제롤 베벨 기어, 마이터 기어, 크라운 기어
<두 축이 평행하지도 교차하지도 않는 기어>
- 나사 기어, 웜 기어, 하이포이드 기어, 페이스 기어, 헬리컬 크라운 기어
문 15. 길이 100cm를 갖는 직사각형 단면의 외팔보에 등분포하중 $\omega =16N/m$가 작용하여 최대굽힘응력이 발생하였다. 이때의 최대굽힘응력 값[$N/m^2$]은? (단, 외팔보 단면의 폭은 8cm이고, 높이는 10cm이며, 보의 자중은 무시한다.)
① $5 \times 10^4$
② $6 \times 10^4$
③ $7 \times 10^4$
④ $8 \times 10^4$
②
<집중하중이 작용할 때 보 공식> | <분포하중이 작용할 때 보 공식> | |||||
$M$ | $\theta $ | $\delta $ | $M$ | $\theta $ | $\delta $ | |
모멘트 | 처짐각 | 처짐량 | 모멘트 | 처짐각 | 처짐량 | |
외팔보 | 1 | 2 | 3 | 2 | 6 | 8 |
단순지지보 | 4 | 16 | 48 | 8 | 24 | 5/384 |
양단고정보 | 8 | 64 | 192 | 12 | 125 | 384 |
<사각형의 도심축 기준 단면계수> <최대굽힙응력>
$Z= \frac{I}{ \frac{1}{2}h } = \frac{bh^3}{6} $ $ \sigma _{max}= \frac{M_{max}}{Z} $
<계산과정>
$M= \frac{ \omega l^2}{2} = \frac{16 \times 1^2}{2} =8N·m$
$Z= \frac{bh^2}{6}= \frac{0.08 \times 0.1^2}{6} = \frac{8 \times 10^{-4}}{6} $
$\sigma _{max}= \frac{M_{max}}{Z}= \frac{8}{ \frac{8 \times 10^{-4}}{6} } =6 \times 10^4N/m^2$
문 16. 금속의 파괴에 대한 종류와 그에 대한 설명으로 가장 옳지 않은 것은?
① 크리프 파괴는 금속의 점탄성적 거동에 의한 변형으로 일어난다.
② 피로 파괴는 외형에 거의 변형을 일으키지 않는 파괴를 보인다.
③ 연성 파괴는 파괴 전 국부적 단면 수축이 생겨 파단되는 것을 말한다.
④ 취성 파괴는 균열면 확대에 소요되는 에너지가 다른 파괴에 비해 크다.
④
<크리프 파괴, Creep Fracture>
고분자 물질인 플라스틱에서 현저히 나타나지만, 철강과 같은 금속재료 또는 콘크리트 등에서도 일어난다. 금속의 점탄성적 거동에 의한 변형으로 일어나게 된다.
<크리프 파괴의 예시>
고무줄에 추를 매달면 순간적으로 고무가 늘어나지만 그대로 방치해두면 시간이 흐름에 따라 고무는 서서히 늘어나는 것, 지상 전선이 오랜 시간 경과 후 늘어지는 현상 등이 있다.
<피로 파괴, Fatigue Fracture>
반복응력이 장시간 가해졌을 때 일어나는 파괴 현상. 외형에 거의 변형을 일으키지 않는 파괴를 보인다.
<연성파괴, Ductile Fracture>
파괴전 Necking이 발생 후 파괴되고, 취성파괴와 비교시 비교적 균일한 큰 소성변형을 통반하여 일어나는 파괴형식이다. 균열전파는 비교적 완만하고 안정적, 파괴단면에 Dimple 형태가 관측된다. 명확한 항복점이 없고, 재료가 소성변형이 충분히 진행된 후에 일어나는 파괴이며 연성이 있는 금속재료를 인장시험시 일어나는 파괴 형식이 대표적이다.
<취성파괴, Brittle Fracture>
취성 파괴는 균열면 확대에 소요되는 에너지가 다른 파괴에 비해 적다. 파괴에 이르기까지 큰 소성변형 없이 균열이 발생하여 그 균열이 상당한 속도로 전파되어 불안정 파괴를 일으키는 형식이다. 불안전파괴란 파괴가 일단 시작되면 하중은 제거되더라도 파괴가 계속 진행되는 파괴를 말하는데, 예를 들면 유리의 파괴가 대표적이며 콘크리트 취성 파괴가 간혹 발생한다. 파괴시 균열이 급격하게 확대되며, 파괴단면은 평평한 것이 특징이다. 일반적으로 알려진 연성파괴 성질의 금속재료에서도 종종 취성파괴가 발생한다.
<취성파괴의 원인>
취성재료는 응력집중에 대한 감도가 매우 높아 인장응력을 받는 부재의 취성재료를 사용할 경우에 발생한다. 또한 상온에서 연성성질을 발휘하는 철강재료라도 저온환경에서는 취성성질로 천이하여 발생할 수 있다.
문 17. <보기>와 같이 압력(P)이 200kPa인 공기가 압력이 일정한 상태에서 500kJ의 열(Q)을 받으면서 팽창하였다. 이러한 과정에서 공기의 내부에너지(U)가 100kJ만큼 증가하였을 때 공기의 체적변화 값[$m^3$]은?
① 1.5
② 2.0
③ 3.0
④ 3.5
②
<밀폐계의 에너지방정식>
$\Delta U=Q-P(V_2-V_1)$
<계산과정>
$(V_2-V_1)= \frac{(Q- \Delta U)}{P} = \frac{(500-100)}{200}=2 $
문 18. 베르누이 방정식(Bernoulli equation)이 적용되는 조건에 해당하지 않는 것은?
① 베르누이 방정식이 적용되는 임의의 두 점은 같은 유선상에 있다.
② 정상상태의 흐름이다.
③ 마찰이 없는 이상유체의 흐름이다.
④ 압축성 유체의 흐름이다.
④
<정압, static pressure>
실제 열역학적 압력으로 유체와 함께 움직이며 측정되는 압력 유체는 흐르고 있기 때문에 유체와 함께 움직이면 상대적으로 정적인 상태이다.
<동압, dynamic pressure>
동압은 고정된 위치에서 측정되는 압력으로 유체의 흐름에 의한 압력. 전압에서 정압을 뺀 값이며 속도가 빠를수록 크게 측정된다.
<전수압, hydrostatic pressure>
실제적인 압력은 아니지만 높이에 따른 유체의 위치에너지를 나타냄
<전압, total pressure>
정압과 동압 그리고 전수압의 합으로 항상 일정하다.
<베르누이 방정식>
$P+ \frac{ \rho V^2}{2}+ \gamma Z=C $
(정압) (동압) (전수압) (전압)
<베르누이 가정>
정상류, 비압축성, 유선을 따라 입자가 흘러야 한다.
비점성(유체입자는 마찰이 없다라는 의미)
문 19. <보기>에 제시된 연강의 응력-변형률 선도에서 A와 E 지점을 옳게 짝지은 것은?
① 비례한도, 극한강도
② 탄성한도, 파괴강도
③ 극한강도, 비례한도
④ 파괴강도, 탄성한도
①
A: 비례한도
B: 탄성한도
C: 상항복점
D: 하항복점
E: 극한강도
F: 파단점
문 20. 재료의 기계적 성질에 대한 설명으로 가장 옳지 않은 것은?
① 경도는 압입으로 생기는 국부적인 소성변형에 대한 재료의 저항성을 나타낸다.
② 인장시험에서 진변형률($ \epsilon $)과 공칭변형률(e)의 관계는$ \epsilon =ln(1+e)$로 표시된다.
③ 숏피닝(shot peening)에 의해 유도되는 표면의 인장잔류 응력은 제품의 피로수명을 향상시킨다.
④ 인장시험에서 재료의 연성을 나타내는 척도는 연신율과 단면감소율이다.
③
<숏피닝, shot peening>
강구로 제작한 숏 볼을 공작물 표면에 압력을 주면서 분사시켜 표면에 압축잔류응력을 남게 하여 피로강도를 증가시키는 가공법
'기계일반 > 서울시 9급(시설관리)' 카테고리의 다른 글
2023년 서울시 9급(시설관리) 기계일반 문제 및 해설 (0) | 2024.04.13 |
---|---|
2022년 서울시 9급(보훈청) 기계일반 문제 및 해설 (0) | 2024.03.17 |
2022년 서울시 9급(시설관리) 기계일반 문제 및 해설 (1) | 2024.03.17 |
2021년 서울시 9급(보훈청) 기계일반 문제 및 해설 (0) | 2024.03.01 |
2021년 서울시 9급(시설관리) 기계일반 문제 및 해설 (2) | 2024.03.01 |
댓글